Errore 302 – Scheda THERMOWATT 740190001703, caldaia Ariston Clas 24FF
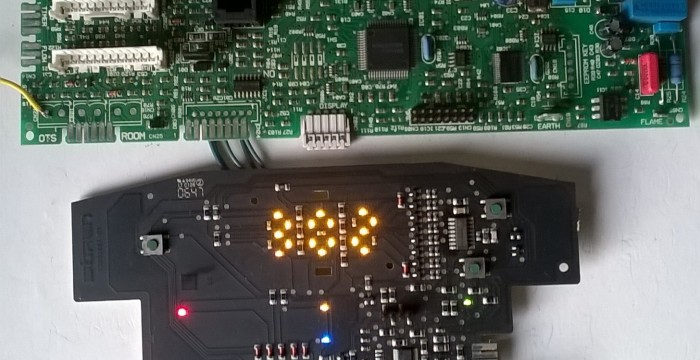
L’errore 302 sulla scheda identificata dalla sigla (Costruttore Numero) Thermowatt 740190001703, ovvero sulle caldaie che la implementano – nel caso in questione una Ariston Class 24FF – porta sempre alla conclusione di una inesorabile sostituzione in toto di tutta la scheda, operazione accompagnata da un costo non indifferente. Ma è sempre così? No, il problema – ovviamente da verificarsi caso per caso – potrebbe essere dovuto ad una “fisiologica” degradazione di una tipologia di componente. Vediamo quale.
Indice - Table of Contents
Il “balletto” dei relè
Navigando in rete si scopre che, almeno per un certo numero di casi, alla visualizzazione dell’errore 302 viene riscontrata una anomalia abbastanza comune relativa ad una continua eccitazione/diseccitazione della bobina di uno o più relè come riportato nel video in łingua spagnola in basso.
Quando mi è stata portata brevi manu la suddetta scheda – data per “persa” da chi mi ha preceduto – è stata riferita l’anomalia riportata nel video, quello che ho definito il “balletto” dei relè unitamente alla visualizzazione dell’errore 302. Ad essere corretti il numero 302 che appare sul display va interpretato come “errore della serie 3 numero 02“.
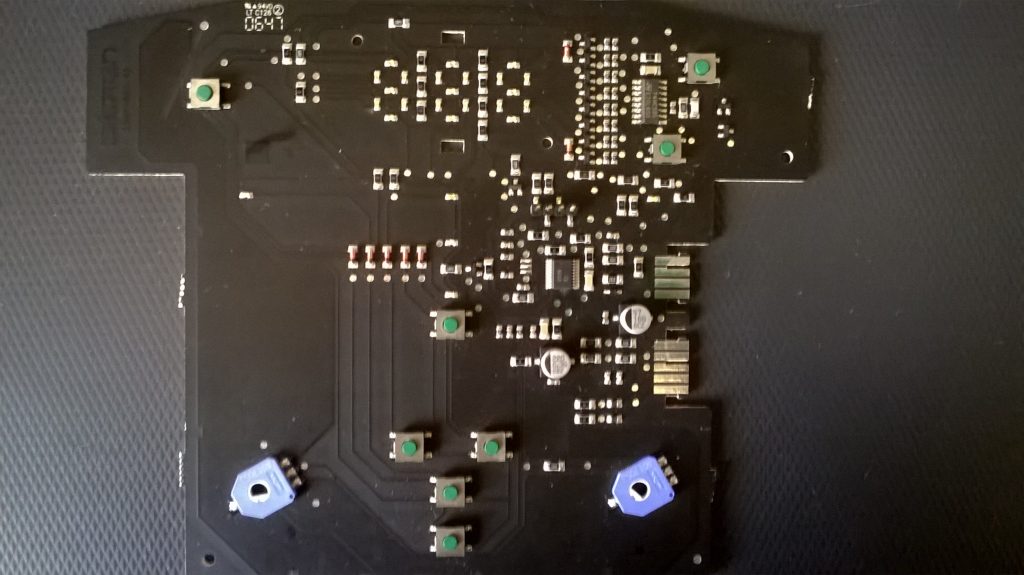
I 3 display a sette segmenti visibili sul frontale della caldaia sono in realtà realizzati, come da immagine in alto, con LED SMD saldati su PCB e attraverso delle guide luce (light pipes) vengono mostrati al frontale come dei classici display a sette segmenti. Per ogni segmento i LED sono pilotati da un classico registro a scorrimento (shift register) della serie 74HC595 (datasheet in basso) nello specifico in package SO16 (Small Outline 16 pin, 8+8) e probabilmente (per non scrivere sicuramente!), per ogni gruppo di LED che definisce una cifra, in modalità multiplexer. L’incertezza è dovuta al non identificato integrato visibile al centro della scheda e riportato di lato (click per ingrandire l’immagine) in un ingrandimento con il microscopio: non si renda conto della data, ogni volta che spengo il microscopio dovrei impostarla, operazione che non eseguo mai. 🙂
La suddetta scheda è molto diffusa e utilizzata in diverse marche di caldaie, non solo in Italia ma, come da video precedente, in nazioni in lingua spagnola, località in lingua russofona così come in zone euroasiatiche (e.g. Turchia 1 e 2). Ovviamente non conosco la problematica delle schede riportate nei video perché non le ho avute sottomano, ma posso riferire la mia esperienza con la stessa scheda e il medesimo errore riportato a display il quale, prima di cercare di risolverlo (se possibile con i mezzi a disposizione), è il caso di capire com’è strutturata e organizzata la scheda.
Conosciamo un po’ la scheda
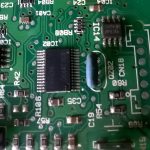
Un’ispezione visuale del PCB e relativa analisi della componentistica evidenzia subito la presenza di due microcontrollori a 8 bit. Con riferimento all’immagine in alto, il primo a destra è un μPD78F0103H (datasheet in basso e immagine a lato, un click per ingrandirla) in package 30-pin plastico SSOP (Shrink Small Outline Package) della nipponica NEC Electronics Corporation, oggi parte della nipponica Renesas Technology Corporation ovvero della Renesas Electronics Corporation. Riporta una piccola etichetta adesiva (non visibile in foto) con su scritto SFKB1FX_2VO 660060005200. L’oscillatore necessario al suo funzionamento è esterno ed è caratterizzato da un filtro ceramico 8MHz a 3 pin.
Errore 302_THERMOWATT_740190001703_uPD78F0103H
I firmware sono memorizzati in due EEPROM/FLASH 93C76 un 4+4 pin in package SOIC (Small Outline IC) della Microchip il cui datasheet è riportato in basso.
93C76
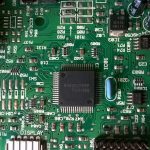
Si è scritto di firmware al plurale in quanto la scheda, come già anticipato, ha un secondo microcontrollore a 8 bit della serie M3803 (datasheet in basso) in contenitore plastico 64 pin 14✕14mm in package QFP (Quad Flat Package). Questo microcontrollore appartiene alla famiglia MELPS 740 della Mitsubishi Electric (invero nel 2002 la Mitsubishi Electric e la Hitachi Ltd spostarono l’industria dei chip a formare la Renesas Technology di cui sopra a cui si aggiunse nel 2010 la NEC Electronics per formare la Renesas Electronics). Anche questo secondo microcontrollore è caratterizzato da un oscillatore esterno costituito da un filtro ceramico a 8MHz. Anche questo integrato reca un’etichetta adesiva (non visibile in foto) con la scritta GL1ATM_4V3 660060007704; probabilmente, poiché si interfaccia con la scheda display, in esso potrebbe essere memorizzato il firmware necessario all’attuazione di alcune funzionalità predefinite (e.g. Comfort, Auto ecc). Seguendo le tracce sul PCB si scopre come i due microcontrollori comunichino tra di loro attraverso le rispettive interfacce UART (Universal Asynchronous Receiver-Transmitter) sfruttando i tipici 2 pin RX e TX.
Errore 302_THERMOWATT_740190001703_M3803xyz
Questo microcontrollore può essere programmato utilizzando la famiglia di programmatori, con annessi adattatori, AF9711, AF9724 o AF9725 della nipponica Flash Support Group. Un esempio di tali programmatori è riportato nel PDF in basso a pagina 8 e 9.
Errore 302_THERMOWATT_740190001703_Programmatori_FSG
Il resto dei componenti è caratterizzato da “circuiteria di contorno” costituita da un pugno di transistor in package SOT23-3 (Small Outline Transistor) caratterizzati da codice SMD A8A, all’atto pratico dei BRT (Bias Resistor Transistor) identificabili con diverse sigle come DTC102, MUN2211T3G, SMUN2211T3G, MMUN2211LT1G, SMMUN2211LT1G e LMUN2211LT1G – associati a diversi produttori come la coreana First Silicon, la statunitense ON Semiconductor o alla cinese Leshan Radio Company – che presentano nel chip la rete di polarizzazione, datasheet in basso. Segue un classico PNP BD138, optoaccoppiatori CNY17F e i tipici array di transistor darlington ULN2003 per il pilotaggio dei relè. Ad alimentare la scheda vi sono quattro tensioni di alimentazione; due a 5V una da integrato stabilizzatore 78M05 in package DPAK-3 a 3 pin e l’altra da integrato 78L05 4+4 pin in package SOIC (Small Outline IC). Seguono una 14V stabilizzata da classico integrato LM317 e una 24V non stabilizzata per le bobine dei relè.
Errore 302_THERMOWATT_740190001703_A8A-DTC101
Analisi del problema
Come anticipato si è in presenza di un “errore della serie 3 numero 02” che sul display appare come Err 302 alternando la scritta Err e il numero 302. Va da se che se non si elimina tale errore la scheda non darà mai alcun consenso al regolare funzionamento della caldaia. Il primo obiettivo è capire il significato di questo errore e quindi da cosa potrebbe essere indotto.
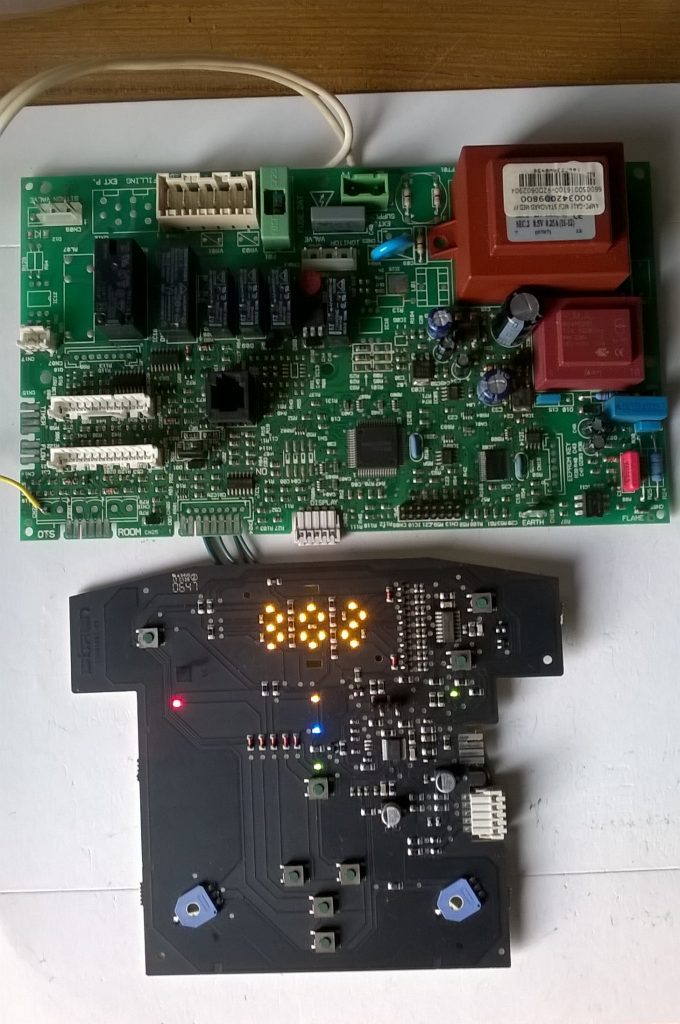
Come visibile dall’immagine in alto, collegata la scheda all’alimentazione di rete il display mostra il numero 302. Da quanto riportato nel manuale e dalle varie ricerche in rete, il motivo sembra essere un errore di comunicazione tra gli elementi GP e GIU, ad esempio:
- Err 3 02: Un caso speciale dell’errore 3 01. Problemi con la scheda EEPROM (memoria non volatile). Se viene visualizzato un messaggio simile, è necessario verificare la EEPROM sulla scheda madre. Entrambe le schede superano il test, ma la connessione tra loro è instabile;
- Err 3 02: GP-GIU exchange error;
- Err 3 02: Errore di comunicazione.
Andando ad intuito la P potrebbe riferirsi alla parola Processore e IU potrebbe essere l’acronimo di Interfaccia Utente (scheda pulsanti e display). Ma la G …? Se qualcuno lo intuisce o lo sa o se la stessa Thermowatt volesse risolvere l’arcano… 🙂
Il terzo errore riportato nell’elenco è quello che si può leggere nel manuale utente a pagina 20, pdf seguente:
In ogni caso qualunque fonte si consideri c’è sempre un elemento comune; un possibile problema di comunicazione tra due “soggetti”, ma dalla spiegazione dell’errore non è dato sapere chi siano questi due soggetti se i due microcontrollori sulla scheda principale oppure tra il secondo microcontrollore e la scheda display; in entrambi i casi, comunque, la comunicazione avviene via UART (Universal Asynchronous Receiver Transmitter). Infatti, seguendo le tracce sul PCB, la seconda UART del microcontrollore M3803 viene utilizzata proprio per la comunicazione con la scheda display.
A conti fatti da qualche parte occorrerà pur partire nel fare qualche verifica. Come primo passo si può iniziare a verificare che i due microcontrollori vengano correttamente “mantenuti in vita” da una stabile oscillazione a 8 MHz ad opera dei filtri ceramici. L’analisi con l’oscilloscopio rileva si l’esistenza dell’oscillazione su entrambi i microcontrollori ma al tempo stesso evidenzia un andamento che lascia un po’ perplessi.
Dagli oscillogrammi, riportati in basso, ottenuti collegando l’oscilloscopio sui pin dei due filtri ceramici, si possono notare degli andamenti non stabili e in ampiezza così come in “larghezza” (nel dominio del tempo) che determinano a prima vista una eccessiva variazione del periodo e di riflesso della frequenza (si misura una variazione di frequenza fino a 60kHz!). Per vedere il campo di variazione si potrebbe impostare la persistenza infinita, ma in questo caso è talmente evidente che non è necessaria. Il tutto con buona pace sulla stabilità di comunicazione tra i vari bus utilizzati dai due microcontrollori compresa la comunicazione via UART tra i due “soggetti” richiamati dall’errore 302, qualunque essi siano questi soggetti.
Il clock jitter
Con il termine jitter si intende una variazione indesiderata nella periodicità del clock durante il funzionamento di un oscillatore. Il jitter può essere visto come una variabile casuale a media nulla. La tipologia di jitter che si presenta davanti potrebbe rientrare, ad esempio, nella Period Jitter o più probabilmente nella Cycle-to-Cycle Jitter. In tale scenario andrebbe osservata (leggasi misurata) la variazione massima tra due periodi di cicli adiacenti su un numero definito di cicli osservati. Il numero di cicli osservati dipende dall’applicazione (e.g. se trattasi di Period Jitter, CtC Jitter ecc). Ad esempio la specifica (standard) JEDEC 65B riporta per il Cycle-to-Cycle Jitter il valore di 1.000 cicli (per maggiori informazioni si può leggere il pdf riportato in basso). Alla frequenza di 8MHz, ovvero un periodo di 125ns (nanosecondi), 1000 cicli equivalgono a 125μs (microsecondi) e per tale lasso di tempo andrebbero fatte le opportune misure, ma in questo contesto un siffatto aspetto non interessa poiché quell’evidente jitter, qualsiasi sia la causa, deve (imperativo) essere eliminato.
Errore 302_THERMOWATT_740190001703_FC1_Jitter_AN-840_Renesas
A tal proposito viene lecito chiedersi se in questo contesto i microcontrollori possano funzionare regolarmente quando il clock presenta un andamento come quello riportato nelle immagini precedenti. Poiché il microcontrollore esegue delle operazioni (leggasi istruzioni) alla frequenza assegnata, un jitter (di qualsiasi natura esso possa essere) che superi la percentuale massima ammissibile può ingenerare delle violazioni del (e sul) ritardo di propagazione determinando così comportamenti non predibili a priori come corruzione dei dati trasmessi su qualsiasi bus, malfunzionamenti, continui reset ecc.
Ebbene si, la colpa è dei soliti noti!
Visto l’inusuale comportamento del clock decido di “chiudere” (aumentare) la base dei tempi dell’oscilloscopio per verificarne il comportamento sul “lungo periodo”, dai 10ms (millisecondi) a salire. Quello che ne viene fuori sono una serie di “buchi” a cadenza periodica nell’ampiezza dell’oscillazione come da immagini in basso; a sinistra vengono spazzati 60ms mentre nell’immagine di destra si punta l’attenzione solo su un buco nell’ampiezza (finestra di 12ms). Chiaramente questo comportamento giustifica “l’alone” visibile sul picco positivo della forma d’onda delle immagini precedenti, un’alone che indica una inevitabile caduta di tensione. Ma dovuto a cosa?
Se si pensa alla periodicità dell’accadimento si potrebbe intuire subito il motivo. Il display segnala l’errore 302 alternando dapprima la scritta Err seguita da 302 e nel mezzo qualche istante dove l’unico assorbimento rimane quello degli integrati e qualche LED SMD di segnalazione presente sulla scheda display; in totale si può quantificare l’assorbimento in qualche decina di milliampere. Quando il display segnala l’errore – sia essa la scritta o la cifra – l’assorbimento sale ad oltre un centinaio di milliampere e di fatto la sezione di alimentazione a 5V si “siede”.
Una immediata verifica sugli stabilizzatori 8L05 e 78M05 certifica il loro corretto funzionamento perché l’abbassamento di tensione lo si ha a cadenza periodica, secondo quanto descritto in precedenza, a monte dei terminali di ingresso dei suddetti. Il cerchio si stringe. Appurato, con la solita metodologia del multimetro in modalità prova diodi, che i due ponti raddrizzatori funzionino correttamente non rimangono che loro; i condensatori elettrolitici!
Eseguo la prova con l’LCR Meter sul primo condensatore in basso – serigrafato C33 – collegato al piedino di ingresso dell’integrato stabilizzatore 78M05 con risultati pessimi (immagine a sinistra, click per ingrandirla); capacità quasi inesistente e ESR (Equivalent Series Resistance) oltre i 75Ω. Per un condensatore da 470μF 25V i valori sono decisamente fuori norma. A destra – un click per ingrandirla – una tabella dei valori massimi che orientativamente si devono riscontrare fissato il valore della capacità e della tensione di lavoro. Il condensatore lo sostituisco così con uno di analogo valore, ma non avendone uno con analoga tensione di lavoro opto per una WV (Working Voltage), ovviamente, superiore e con caratteristiche misurate e visibili in basso. Il rientro del valore nella tolleranza e una ESR pari a 80mΩ; un tipico condensatore a basso ESR utilizzato negli alimentatori switching (SMPS, Switched Mode Power Supply).
Eseguo la prova anche su tutti gli altri condensatori visibili senza che questi mostrino alcun problema. L’ultimo condensatore serigrafato con la sigla C29 invece non da segni vitali. Non esiste nulla, né capacità, né ESR e questo a qualsiasi frequenza delle 5 (da 100Hz a 100kHz) supportate dall’LCR meter. Il motivo diventa chiaro quando vado per rimuoverlo dal PCB; un piedino è letteralmente sganciato dal corpo del componente. Ovviamente da sostituire.
Ancora non è finita!
Saldati provvisoriamente i condensatori come da foto precedenti e rianimando (alimentando) la scheda ecco che magicamente (si fa per dire…) il temibile errore 302 sparisce lasciando il posto ad un comprensibile errore 608 e talvolta, ripetendo l’accensione, all’errore con codice 6P2 rispettivamente con significato, come da tabella degli errori visibile a pagina 19 del manuale della caldaia riportato in formato PDF in alto, di Mancato consenso pressostato fumi con ventilatore attivo e Apertura pressostato fumi durante normale funzionamento.
Errori “comprensibili” perché, di fatto, si sente il relè che attiva il ventilatore animarsi, ma manca il consenso del pressostato fumi non essendo collegato durante la prova di alimentazione della scheda. Lo schema di cablaggio del pressostato fumi nonché di tutti gli altri dispositivi di gestione e controllo (e.g. ventilatore, termostato limite, termostato ambientale, elettrovalvola, pompa acqua, accenditore ecc) è riportato a pagina 13 del manuale. Volendo, allora, effettuare una prova più completa è possibile sostituire ogni singolo componente del sistema con lampadine/LED laddove si hanno i consensi e alimentazioni a 230V dai relé (ad esempio al posto del ventilatore fumi si può collegare una lampadina che possa mostrarne la corretta alimentazione) e con interruttori normalmente aperti o chiusi nel caso di termostati, pressostati ecc (ad esempio il pressostato fumi con un interruttore chiuso che ne simula il consenso), esattamente come riportato nel video in lingua russofona in alto.
In ogni caso una verifica del clock con l’oscilloscopio nei medesimi punti (riferiti a massa) delle misure precedenti rileva un andamento pulito senza alcun “artefatto” come da immagini che seguono.
È tempo di collegare la scheda alla caldaia, ma con grande sorpresa anche cablando il pressostato fumi, il ventilatore fumi, il termostato limite e ambientale, l’elettrovalvola e tutto il resto, ecco spuntare di nuovo l’errore 6P2! Il motivo è a vista ed è dato dal mancato consenso del pressostato fumi dovuto al non funzionamento del ventilatore fumi. In sostanza il consenso al relè del ventilatore fumi viene fornito ma la ventola non parte! Appurato in loco che la ventola (alimentata a 230V) non avesse alcun problema l’attenzione si è spostata sul relè per il quale si sentiva si il “click” di attivazione, ma non contattava! Problema? Contatti relè carbonizzati tali da non chiudere il circuito! Sostituito il relè – adottando le misure di sicurezza del caso con guaine termorestringenti per l’isolamento dei contatti a vista – e rimontata la scheda, la caldaia si avvia senza problema e attiva tutte le funzioni di regolazioni e preimpostate confermando la non corruzione dei firmware caricati in azienda nelle due EEPROM 93C76.
Costo complessivo componenti 4,50€ …nel mio caso li avevo tutti quindi 0,00€. 🙂
Per i curiosi, il modello del relè in questione è un FTR-F3AA024E (datasheet in basso) della nipponica Fujitsu, esattamente come gli altri 3 relè a singolo polo visibili nell’immagine in alto a sinistra (un click per ingrandirla).
Errore 302_THERMOWATT_740190001703_FTR-F3AA024E
Conclusioni
Non sempre l’errore 302 sottintende la sostituzione in toto dell’intera scheda. Naturalmente occorre valutare il problema caso per caso ma quanto meno una misura dei parametri principali (andamento clock, livello tensioni, misura di eventuali delta in frequenza e/o in tensione ecc) può far risparmiare un biglietto da 100€ per l’acquisto di una nuova scheda e un biglietto da 50€ per il servizio cambio.
Chi si dovesse trovare nella medesima condizione prima di pensare al cambio della scheda potrebbe far fare un controllo di questo tipo da qualche conoscente dotato di un minimo di strumentazione (alla fine ciò che occorre è un multimetro e un oscilloscopio anche analogico).
Ultima nota sui componenti sostituiti. Va da se come non debbano essere lasciati liberi di muoversi. Medesima precauzione vale non solo per i condensatori ma anche per le grosse induttanze, termistori e varistori lato tensione di rete. È il caso di bloccare tali componenti con un goccio di colla a caldo oppure con un adesivo siliconico bicomponente/monocomponente.
Questa accortezza serve a fissare meccanicamente componenti pesanti o fragili alla scheda PCB ad evitare che si muovano a causa delle vibrazioni rompendo altresì i terminali e/o le stesse saldature, fenomeno noto come cracking solder joints.
Non utilizzare mai silicone acetoxy (silicone acetico) poiché durante la polimerizzazione emette acido acetico corrodendo il metallo sottostante, ovvero le piste in rame del PCB. Se si dovesse optare per il silicone nel bloccaggio dei componenti in luogo della colla a caldo, assicurarsi sempre di utilizzare silicone neutro o di grado elettronico, tipicamente di colore bianco.