Costruire un monitor dallo schermo di un portatile dismesso
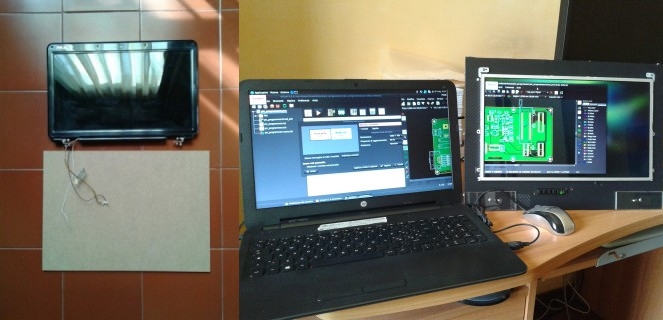
Indice - Table of Contents
Introduzione
Il tutto ha inizio da una lastra di MDF (Medium-Density Fibreboard) di spessore 6mm e formato A3 (42×29,7cm) e dalla sigla B156XW02 di uno schermo LCD. L’obiettivo è il riuso (tipico termine tanto caro in un contesto di programmazione ad oggetti, e.g. Java, Python&C.) del suddetto schermo recuperato da un vecchio portatile (anno 2010), nello specifico un ASUS K51A per il quale ho già indicato un possibile riuso del pacco batterie e nello specifico delle batterie in esso contenute (e.g. Li-Ion nel formato 18650 da utilizzarsi in torce flashlight).
Quella che segue è una mia versione del riutilizzo dello schermo che possa prevederne l’applicazione come secondo schermo in un computer desktop/portatile (e.g. molto comodo nell’uso di programmi CAD quando si è sprovvisti di un monitor di una certa dimensione, minimo 24 pollici a salire), monitor per giochi o adottabile anche come schermo per piccoli computer come il Raspberry PI. Parliamo di uno schermo il cui costo – al netto di offerte – parte da circa 70€ a salire, quindi perché buttarlo quando può essere riciclato (leggasi riutilizzato) per lo scopo per il quale è stato realizzato?
Va da se che la procedura riportata nel seguito è adottabile con qualsiasi schermo anche non appartenente ad un portatile ma, ad esempio di un monitor propriamente detto. In questo caso si ha già disposizione il case nel quale inglobare il controller, eventuali altoparlanti, pulsanti, ricevitore IR ecc.
Rimuovere lo schermo
Nella grande rete è possibile trovare diverse soluzioni di riuso ognuna delle quali può piacere o meno ma dalle quali è possibile trarne suggerimenti per realizzare un proprio monitor (DIY – Do It Yourself).
Nel seguito è presentata la mia versione la cui prerogativa principale era quella di non utilizzare colle di alcun tipo (tranne per la pellicola adesiva che già ce l’ha di suo!) ma affidarsi a minuterie varie (e.g. distanziatori esagonali di zinco/acciaio e di gomma di varie dimensioni, dadi, rondelle, viti ecc) per mantenere ogni singolo elemento necessario alla sua realizzazione.
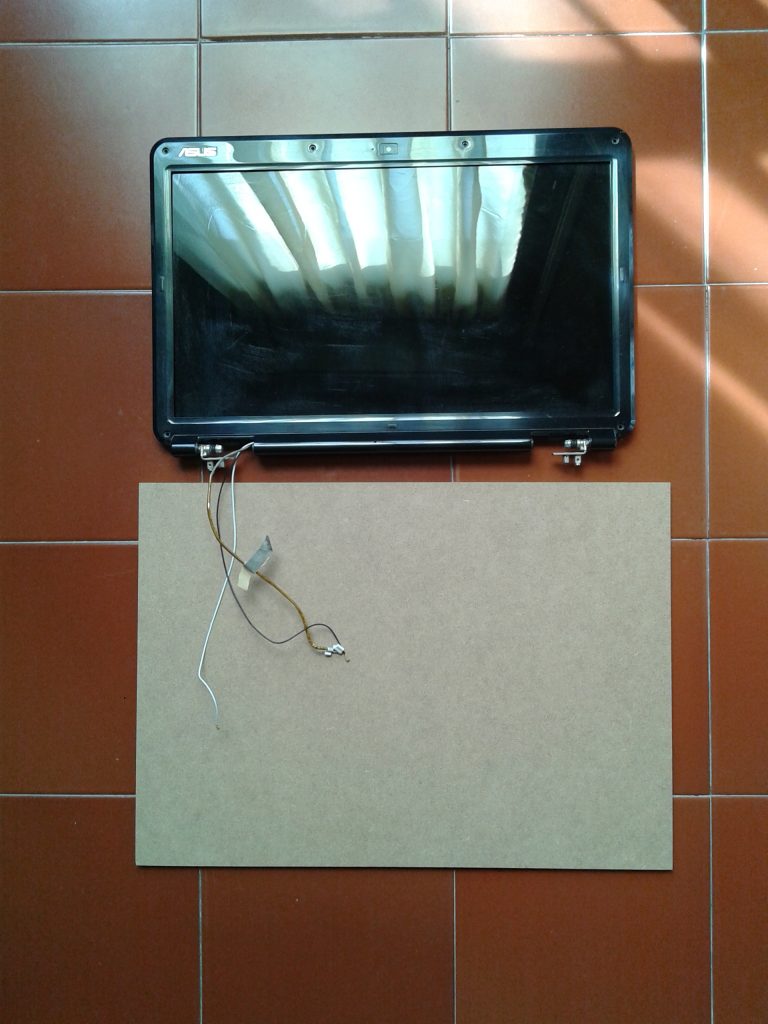
Il punto di partenza vede la rimozione dello schermo dividendolo di fatto dal portatile (o di quel che ne resta). Si dovrà operare con una certa attenzione al fine di non danneggiarlo e nelle parti meccaniche, che potranno essere riutilizzate come fermi ma, soprattutto, nelle parti elettroniche che renderebbero lo schermo di fatto inutilizzabile, da buttare! In basso ne è riportato il datasheet.
Per i più curiosi in basso è riportata una galleria di immagini (cliccare su una fotografia per ingrandirla) del retro dello schermo con l’elettronica di controllo e di potenza presente su un Flex PCB protetto da una pellicola trasparente.
Smontato lo schermo fortuna vuole che i fermi meccanici (dal colore e dalla leggerezza sembrerebbero in magnesio/alluminio) presentino una simmetria su tutta la larghezza: questo permette di rovesciare di 180° la striscia di magnesio con la quale è possibile ancorare lo schermo su due lati al pannello MDF mantenendo così i reofori più bassi ed evitando viti sporgenti oltre l’altezza dello schermo (verificare con le figure in basso).
LCD Driver Controller
Una volta che si ha lo schermo LCD è possibile accedere alla sua sigla (modello di schermo) presente sulla riga Model No dell’etichetta adesiva: B156XW02 V.2.
Nota la sigla occorre andare alla ricerca di una LCD controller board idonea a pilotare il modello di schermo. Si vuole infatti ricordare che nel portatile il controller è integrato sulla scheda madre pertanto non è possibile collegare direttamente un cavo VGA, HDMI ecc direttamente all’elettronica presente dietro lo schermo LCD. L’uscita del controller andrà a collegarsi al connettore da 40 pin (nel caso specifico) presente sul retro dopo aver rimosso delicatamente e con attenzione quello già presente (come visibile nella galleria in alto).
Utilizzando un qualsiasi motore di ricerca, inserendo la stringa (senza doppi apici) “B156XW02 controller board” è possibile accedere a diversi risultati.
Attenzione: gli schermi LCD sono riutilizzati più e più volte nelle varie marche di portatili, modelli uguali ma versioni differenti! Infatti oltre alla sigla – B156XW02 nel caso in questione – occorre prestare attenzione anche alla versione questo perché con il tempo vengono rilasciate più versioni dello stesso schermo. Per il modello in parola si ha la versione 2.0, ma al momento di scrivere queste righe tale schermo LCD è arrivato alla versione 6 il quale si differenzia dalla versione 2, per il fatto che il controller è dotato di PCB a parte con funzioni di LED Boost driver necessario a pilotare la LED lightbar, la cosiddetta “retroilluminazione”; in realtà trattasi di una striscia di led che può essere presente su 1 o 2 lati dello schermo. Ebbene, nel caso dello schermo B156XW02 V.2, il LED Boost driver è già integrato nel Flex PCB dell’LCD.
Possono esserci controller un po’ più sofisticati, e.g. completi di telecomando ad infrarosso – e quindi anche di un ricevitore che si collega al controller – che permettono di impostare i parametri dello schermo da remoto, come se si stesse utilizzando un usuale telecomando per TV. Naturalmente il costo di queste versioni è sensibilmente maggiore. In definitiva il controller driver utilizzato in questo specifico caso è un 1366×768 LED LCD Controller Driver Board completo di ingressi HDMI, DVI, VGA, PC Video, PC Audio e uscita audio stereo amplificata (2W+2W). In basso ne viene riportato il datasheet.
E, al solito per i più curiosi, una galleria fotografica dove ogni singola fotografia punta l’attenzione su qualche particolare interessante della scheda.
Nella seconda fotografia una visione generale della scheda lato componenti, nella sesta il retro. Nella quarta fotografia è puntata l’attenzione sul cuore della scheda l’integrato NT68676 un Display Driver ICs per display LCD della Taiwanese Novatek Microelectronics Corp coadiuvato da una Serial Flash da 4Mbit – visibile in alto a destra – per lo storage del firmware, di preciso un integrato GD25Q40CTFG in package SOP (Small Outline Package) 8 pin 150mil della Cinese GigaDevice, di seguito il datasheet.
Nella terza immagine è visibile un Synchronous Step-Down Converter TPS54329 della Texas Instruments necessario per ridurre il livello di ingresso ai valori logici utilizzati dalla scheda (datasheet in basso).
Spostandosi dall’altro lato della scheda (immagine numero cinque) è possibile trovare l’integrato TDA7496L della Taiwanese Unisonic Technologies. Trattasi di un amplificatore di potenza con uscita stereo 2+2 Watt operante in classe AB che implementa alcune funzioni come il controllo lineare del volume, il mute e la stand-by. Un IC principalmente utilizzato per applicazioni TV e nei monitor. Le caratteristiche complete è possibile leggerle nel datasheet in basso.
A completare l’elenco dei componenti attivi seguono 3 regolatori della serie 1117 (datasheet in basso) della statunitense Advanced Monolithic Systems; uno da 1,8V in package SOT-223 (Small Outline Transistor) e gli altri due da 3,3V in package TO-252 (Transistor Outline).
Infine 5 componenti in package SOT-23 (Small Outline Transistor) dalla cui sigla H1A parrebbero essere dei BJT NPN sigla MMBT3904/BR3DG3904M – datasheet in basso – della Blue Rocket Electronics, in questo contesto utilizzati come switching.
Primo test e consumi di massima
Il controller necessita di un’alimentazione di 12V continui, pertanto si rende necessario per un primo test un alimentatore stabilizzato in grado di assicurare la suddetta tensione. La conferma del valore della tensione di alimentazione la si può ottenere dal lato saldature della scheda sulla serigrafia del PCB sotto il connettore di alimentazione dove è riportato chiaramente 12V (fotografia di lato, click per ingrandirla).
Attenzione: utilizzando un comune multimetro assicurarsi sempre quale sia la parte del connettore collegata alla massa e quindi, per esclusione, a quale contatto del connettore corrisponde il positivo di alimentazione! Questo perché non tutti seguono la medesima regola che generalmente vede il polo negativo associato all’involucro esterno del connettore e il contatto centrale associato al polo positivo. In alcuni casi questa regola viene invertita pertanto eseguire sempre un controllo prima di alimentare qualsiasi scheda!
Effettuata la verifica, il primo passo è condurre un test per verificarne il corretto funzionamento anche della pulsantiera. In genere, come lingua predefinita per i menù, in questi prodotti viene utilizzato il Cinese ma la localizzazione è in diverse lingue compreso l’italiano che è possibile impostare agendo sugli appositi pulsanti i quali portano in serigrafia sul PCB le funzioni. Come già anticipato questa parte verrà sostituita con una millefori e pulsanti/led di recupero poiché l’altezza dei pulsanti non è sufficiente a fuoriuscire dal pannello MDF. Non solo, ma, come si vedrà, anche il connettore in dotazione è stato sostituito poiché di qualità piuttosto bassa.
Per condurre un test preliminare è sufficiente collegare il connettore LVDS (Low-Voltage Differential Signaling) maschio a 40 pin in dotazione del video controller (figura a lato, click per ingrandirla) al connettore femmina presente dietro lo schermo. È stato già detto come in questa versione il LED Boost driver risulti integrato. In altri modelli, qualora nonlo fosse, occorrerà provvedere al collegamento del boost utilizzando gli appositi connettori presenti. Effettuati i collegamenti “controller LCD→schermo LCD” occorre collegare un ingresso video tra i vari HDMI, VGA o DVI proveniente, ad esempio, da un portatile con aperto un documento PDF. Verificato il collegamento “sorgente video→controller LCD” non resta che attivare l’alimentazione a 12V per vedere l’immagine presente sulla sorgente video duplicata sullo schermo LCD recuperato.
In genere, come impostazione predefinita, si ha una visualizzazione caratterizzata dalla medesima immagine su tutti i monitor pertanto non si dovrebbe avere difficoltà alcuna a visualizzare ciò che viene aperto sul portatile o computer desktop che sia.
Inoltre questo test preliminare permetterà di effettuare una stima di massima dei consumi lato rete fissato un certo valore cautelativo del rendimento di un futuro alimentatore. L’alimentatore con uscita regolata a 12V e collegato direttamente al controller mette in luce un consumo di circa 630mA per un totale di 7,5W, solo per lo schermo da 15,6 pollici. Considerando i 2W+2W dell’uscita audio, un buon flyback 230V->12V da 1,2A – con rendimento almeno (!) dell’85% – dovrebbe essere più che sufficiente. In definitiva circa 17W lato rete, ovvero poco più di 1W per pollice nel worst case (caso peggiore). Un consumo non bassissimo tale da insignirlo con una eventuale classe energetica A+++, ma sufficientemente basso da farlo rientrare comunque in una classe A!
Dalle sagome alla pellicola adesiva
Verificato il corretto funzionamento occorre temoraneamente accantonare la parte elettronica per iniziare a lavorare sul pannello MDF. Qui non c’è molto da dire: il tutto dipende dai propri obiettivi, dal materiale che si ha a disposizione (minuteria meccanica vs colla) e dagli utensili; nel caso specifico è stato utilizzato un trapano avvitatore a batterie Beta 1972/12 con un paio di frese per legno laddove necessarie (e.g. sagomare il pannello per ospitare la pulsantiera e il passaggio del connettore/cavo LVDS). Ho inoltre utilizzato gli altoparlanti del vecchio portatile al fine di rendere il monitor “autonomo” anche dal punto di vista audio ma con la possibilità di effettuare una commutazione verso una fonte esterna di amplificazione (e.g. classiche casse per computer o dispositivi simili). Gli altoparlanti recuperati dal portatile sono a tutti gli effetti delle minuscole casse – della statunitense Altec Lansing – che sfruttano la tecnica del bass reflex (notare la piccola apertura quadrata vicino al minuscolo altoparlante nella foto in alto a sinistra, click per ingrandirla) e ciò, come è ben noto, al fine di ottenere, a parità di potenza, più volume e pressione sonora dimezzando l’escursione del cono dell’altoparlante rispetto ad una cassa chiusa. Dal punto di vista audio una tecnica che a me personalmente non piace molto ma, che piaccia o meno, rimane una soluzione obbligata per dispositivi portatili viste le ridotte dimensioni in gioco! Di seguito una galleria fotografica di alcuni passaggi.
Naturalmente occorre prendere le corrette dimensioni di ogni oggetto che si intende aggiungere, la posizione dei fori, valutare la lunghezza dei cavi per un miglior posizionamento del controller sul retro, verificare gli ingombri (e.g. gli altoparlanti non devono essere posizionati vicini ai lati del controller altrimenti sarà impossibile effettuare una connessione VGA, DVI o HDMI che sia).
Nel caso in parola – come già detto – ho preferito eliminare la pulsantiera in dotazione del controller per sostituirla con un PCB millefori con sopra saldati dei pulsanti recuperati tempo addietro da un vecchio TV CRT (Cathode-Ray Tube) e due diodi led rettangolari (verde e rosso). Il motivo è presto detto: l’altezza dei pulsanti era troppo ridotta e i pulsanti non uscivano sul lato frontale dell’MDF.
Altra considerazione. Si ricorda di non buttare le cerniere del display poiché, se adeguatamente realizzate, possono fungere da piedi regolabili per l’inclinazione del futuro monitor “home made”. Nel caso in questione sebbene sia stato possibile recuperare e assemblare le suddette cerniere – come visibile nelle figure – alla fine sono risultate un po’ piccole e hanno necessitato di una aggiunta supplementare di qualche cm (non visibile nelle fotografie) con aggancio a vite negli appositi fori rendendo il tutto più stabile. Come sistema regolabile in inclinazione volendo è possibile riciclare anche cardini di porte o di ante per mobili …se non eccessivamente “grezze”!
A questo punto è stata rimossa tutta l’elettronica, le viti e i dadi e con un po’ di alcol denaturato ho pulito entrambe le superfici per prepararle alla colla (inevitabile!) della pellicola adesiva. Per tale operazione – non proprio facile se non si ha un minimo di pazienza – suggerisco la visione di alcuni video presenti sul canale YouTube ARTESIVE oltremodo rivenditore (ovviamente non l’unico in Italia!) di pellicole adesive. Personalmente avevo già una pellicola tecnica adesiva ad effetto carbonio (figura in alto a sinistra, click per ingrandirla) ma, come è facile verificare, se ne possono acquistare di diversi tipi e colori in funzione del proprio gusto.
La galleria fotografica che segue illustra alcuni dei passaggi. Gli inserti in PVC sui lati bassi del monitor sono stati necessari per bloccare le cerniere che fungono da piedini regolabili. Pertanto oltre alla loro funzione di permettere il bloccaggio delle cerniere hanno anche una funzione “visiva” poiché permettono di variare i riflessi di ciò che da la carta adesiva scelta conferendo all’insieme un minimo di eleganza.
Due note a margine della precedente galleria fotografica. La prima. Per mantenere la pellicola su ogni lato ho utilizzato 3 piccole viti del diametro di 2 mm di tipo autofilettanti (creano la maschiatura di un foro precedentemente creato – 1,5mm – quando inserite). La seconda. Come test ho provato a dare un riflesso differente alla parte dove sono posizionati i due pezzi di PVC utilizzando spezzoni di pellicola adesiva ruotata di 180° rispetto alla posa sul pannello in MDF. Effettivamente il riflesso è differente e spezza in maniera gradevole rispetto al resto …peccato che avessi finito la pellicola e quindi per coprire tutta la parte ho dovuto fare degli spezzoni un po’ più corti (parte in basso a sinistra del pannello).
A questo punto è arrivato il momento di assemblare il tutto. Prima di questa operazione ho dovuto, gioco forza, cambiare il connettore della pulsantiera poiché di bassa qualità e nella crimpatura così come nella tipologia di cavi utilizzati (figura a lato, click per ingrandirla): 3 piccoli filetti di rame per ogni cavo tale da spezzarsi dopo un paio di prove!
Nel cambio di connettore ho fatto un lavoro di fino, forse un po’ eccessivo (figura in basso), coprendo le saldature delle aggiunte con guaine termorestringenti (gialle e rosse) con pistola della hot air soldering station regolata a 105°C per un totale di una 15ina di secondi a guaina. La temperatura più idonea è in genere riportata sulla confezione delle guaine direttamente dal produttore: per quelle in parola la temperatura andava da un valore superiore agli 85°C – mantenimento oltre i 30 secondi – fino ai 125°C con un mantenimento di 10-15 secondi. Infine per ogni cavo è stata aggiunta una etichetta recante la sua funzione (Led verde, On/Off ecc).
Di seguito una galleria fotografica che riporta i passi seguiti nell’assemblaggio di tutti i pezzi e subito in basso i commenti alle diverse fotografie.
Notare il nuovo connettore nell’immagine numero 2 e i cablaggi con la pulsantiera nella numero 3. Nell’immagine numero 4 viene evidenziato il fermo del connettore ad evitare che si sfili. Il suddetto fermo è stato riciclato da un pezzo di distanziatore di spugna adesiva presente tra lo schermo e plastica nello chassis del portatile. È possibile utilizzare anche un buon nastro isolante. Nell’immagine numero 5 la vista d’insieme sul retro: notare in alto al centro la millefori con deviatore che permette di attivare gli altoparlanti integrati oppure di deviare il segnale verso un amplificatore esterno da collegarsi tramite classico jack stereo da 3,5mm. Inoltre notare la presenza di quattro distanziatori esagonali che dovranno bloccare il futuro PCB che dovrà ospitare un convertitore DC/DC da 5V a 12V (USB3) e un flyback di rete 230V/12V@1,2A, entrambi in fase di progettazione. Saranno riportati su questo sito una volta terminati. I 4 distanziatori esagonali avvitati sul controller serviranno a mantenere la futura copertura. Infine, l’immagine numero 6 la vista d’insieme del frontale.
Prova finale
Non resta che provarlo. Nelle immagini in basso il “nuovo monitor” in funzione via VGA da un portatile HP con installata la distribuzione GNU/Linux Mageia 8 e ambiente desktop Mate. Nella prima immagine, tramite il sistema di configurazione dello schermo, si deseleziona la casella Stessa immagine in tutti i monitor. Così facendo ogni monitor potrà avere la propria immagine. All’atto pratico è come se il “nuovo monitor” fosse un prolungamento destro del monitor del portatile; ciò che sparisce a destra del monitor del portatile appare a sinistra del “nuovo monitor” (immagine numero 2). Infine nell’immagine numero 3 il programma KiCAD con a destra – nel “nuovo monitor” – il PCB e a sinistra – nel monitor del portatile – la sua visualizzazione in 3D. In questo specifico caso la risoluzione di entrambi i monitor è la medesima pertanto non si hanno deformazioni; 1366×768, ovvero un rapporto d’aspetto pari a 16:9.
Excellent post. I was checking continuously this blog and I’m impressed!
Extremely helpful information specially the remaining section 🙂 I take care of such info much.
I was looking for this certain information for a long time.
Thank you and good luck.
I am in fact delighted to read this blog posts which contains lots of valuable information, thanks for providing such statistics.